Producing glass and stone wool
The production of mineral wool insulation is a process of consecutive melting, fiberisation, curing, cutting and packaging.
Precisely measured quantities of natural raw materials like basalt, diabase and dolomite (stone wool) and sand, limestone and soda ash (glass wool) – and an increasing amount of secondary (recycled) raw materials, cullet and slag – are sent from feeders into a melting furnace.
The growing raw material input from recycling comes from the internal production process, external construction and installation cut-offs as well as increasing amounts of post-consumer renovation and demolition waste – or recovered secondary raw materials from diverse other product applications. Using secondary raw materials requires less energy and is thus a natural incentive for recycling. Recycled glass cullet constitutes up to 85% of raw material input for glass wool production while recycled briquettes and integrated melting technology allow for direct use of secondary slag and post-consumer waste in stone wool production.
In the melting furnace, the carefully selected, composed and weighed raw material batch is melted at high temperatures, typically between 1,300°C to 1,500°C. The exhausts created during this process are filtered and flue gases are cleaned to minimise any environmental impacts. Water use in the process is generally confined to closed circuit systems. This reduces freshwater consumption and avoids polluted water discharges.
The melted raw materials from the furnace then fall onto rapidly rotating flywheels (cascade spinning or rotary spinning) shaping them into fibres. Small quantities of binding agents are added to keep the fibres together and add to strength and mechanical properties.
The production process allows for calibration of both structure and density of the final product to fit the required performance of the specific product application. The mineral wool insulation then takes its final shape in a curing oven at around 200°C.
Towards the end of the production line, the mineral wool insulation is cut into the required size and shape – rolls, batts, boards – or it can be customised to specialised products. Off-cuts and other mineral wool scraps are recycled back into the production process, which further reduces inputs and energy requirements.
Thanks to its impressive elasticity, mineral wool insulation can be compressed during packaging to reduce its volume. This makes it cheaper and easier to handle – and leads to lower carbon emissions in transportation.
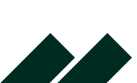